射出成形における超薄肉成形技術
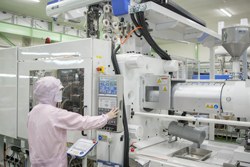
現在、射出成形による薄肉製品といえば0.4~0.5mmが主流。0.4mm以下の壁は厚く、多くの企業が超薄肉に挑戦しては実現できずにいました。今回その技術を構築したのが『アスカカンパニー』。開発部門を持たない東北工場が、現場の経験を生かし0.3mmという数字を可能にしたのです。マネージャーの安彦さんと製造課マネージャー兼工場長代行の野村さんは、開発の背景をこう話します。
「弊社ではプラスチックの薄肉容器やフタなどを主に製造しています。開発はトイレタリー用品の要請がきっかけでしたが、限りある資源を有効に使い地球に優しいものづくりを目指すことは当社の理念でもあります」(安彦さん)。
「工場ですから、24時間体制で既存の受注生産をしながらの開発でした。自分たちでできることは何でもやる、ということも会社の方針。社員の協力体制もあり、無事に完成させることができました」(野村さん)。
素材・機械メーカーとともに試行錯誤。
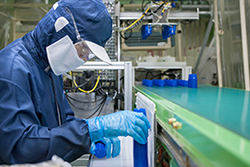
0.3mm以下の製品を生産するのに一般的なシート成形の場合は、厚さを均一にすることが難しく目指す寸法精度に至らないことがあります。また、精度の高い密閉型を使う方法では、薄くなればなるほど細部に樹脂が流れず未充填になってしまいます。射出成形で樹脂を均一に流し安定した速度で生産するため、金型・成形機・原材料の各メーカーの協力は不可欠でした。
「金型は圧力により目に見えない歪みや曲がりが生じ、取り出す際に動かすことで摩耗します。しかし、樹脂を全体にまんべんなく流すには金型の歪みや摩耗は許されません。そこで金型メーカーとは、耐久性のある金型の製造と動かさず離型させる方法を互いに提案しました。成形メーカーには金型が閉まったときの歪みを矯正する構造をつくってもらい、原材料メーカーとは新しいグレードの試作を重ねました」(安彦さん)。
今回の開発は成形技術だけではありません。生産品をすべて検査する測定機も同時に製作。未充填の箇所や穴の有無などをチェックし、品質保証をつけることで本当の意味で射出成型による0.3mmの超薄肉成形品が完成したのです。
「全数検査の機械を開発しない限り品質保証はできませんから、検査機ができたときは、これで自信を持って世の中に出せる、と思いました」(野村さん)。
現場の力を生かして技術の進化に挑む。
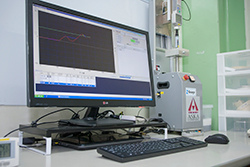
「いい機械があっても使いこなせなければ意味がない。開発だけでなくものづくりのレベルを上げ、現場の経験を次に生かすことが大切なのです」と安彦さん。『アスカカンパニー』では、今回の技術をさまざまな製品へ展開させ、これまで以上に環境に優しいものづくりに力を入れる予定です。
「自社開発の測定器も販売していきたいですし、この技術で得たものを外に発信しようと考えています。産学連携や地域貢献も積極的に行いたいですね」(野村さん)。
また、技術の発信と開発には「みやぎ優れMONO」認定による特典も一役買っています。
「宮城県産業技術総合センターにある高価な測定機器を、無料または優遇して活用させていただきました。展示会の出展費用を助成いただき、それにより多くの出会いに恵まれたこともうれしく思っています」(野村さん)。
(2013年12月 インタビュー)